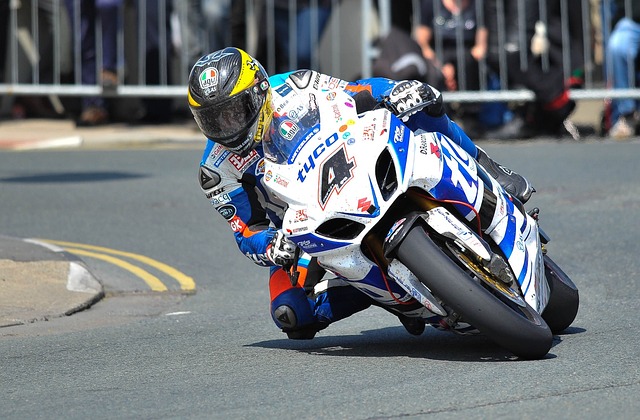
Continuous Improvement
Understanding Continuous Improvement
Continuous improvement, often referred to as CI, is a philosophy that focuses on the ongoing enhancement of products, services, or processes. It’s a mindset that encourages organizations to constantly seek ways to improve efficiency, quality, and overall performance. Whether you’re in manufacturing, software development, or any other field, embracing continuous improvement can lead to significant benefits.
The Core Principles of Continuous Improvement
At its heart, continuous improvement is about making small, incremental changes that add up over time. Here are some key principles:
- Customer Focus: Always prioritize the needs and feedback of your customers. Their experiences should guide your improvements.
- Data-Driven Decisions: Use data and metrics to identify areas for improvement. This helps in making informed choices rather than relying on gut feelings.
- Employee Involvement: Engage employees at all levels. They often have the best insights into the processes they work with daily.
- Incremental Changes: Focus on small, manageable changes rather than sweeping reforms. This makes it easier to implement and track progress.
Popular Methodologies for Continuous Improvement
There are several methodologies that organizations can adopt to facilitate continuous improvement. Here are a few of the most widely used:
- Lean: This approach aims to reduce waste and enhance efficiency by streamlining processes. Lean focuses on delivering value to customers while minimizing resources.
- Six Sigma: A data-driven methodology that seeks to improve quality by identifying and removing the causes of defects. Six Sigma uses statistical tools to analyze processes and drive improvement.
- Kaizen: A Japanese term meaning "change for better." Kaizen emphasizes continuous, incremental improvement in all aspects of life, including business. It encourages a culture where all employees are involved in suggesting improvements.
- PDCA Cycle: The Plan-Do-Check-Act cycle is a four-step model used for continuous improvement. It encourages organizations to plan changes, implement them, check the results, and act on what they learn.
Benefits of Continuous Improvement
Implementing continuous improvement strategies can yield numerous benefits for organizations:
- Enhanced Efficiency: Streamlining processes can lead to reduced costs and faster delivery times.
- Improved Quality: Regularly refining processes helps in minimizing errors and defects.
- Increased Employee Engagement: When employees are involved in the improvement process, they feel more valued and motivated.
- Better Customer Satisfaction: By focusing on customer feedback, organizations can enhance their offerings and improve customer loyalty.
Implementing Continuous Improvement in Your Organization
To effectively implement continuous improvement, consider the following steps:
- Assess Current Processes: Start by evaluating existing processes to identify areas that need improvement.
- Set Clear Goals: Define what you want to achieve with your continuous improvement efforts.
- Engage Employees: Foster a culture of improvement by encouraging employees to share their ideas and insights.
- Monitor Progress: Use metrics to track improvements and make adjustments as necessary.
- Celebrate Successes: Recognize and reward improvements, no matter how small. This reinforces the continuous improvement mindset.
Conclusion
Continuous improvement is not just a buzzword; it’s a vital strategy for organizations looking to thrive in today’s competitive landscape. By embracing methodologies like Lean, Six Sigma, and Kaizen, and fostering a culture of improvement, organizations can enhance efficiency, quality, and customer satisfaction. So, why not start today? 🚀