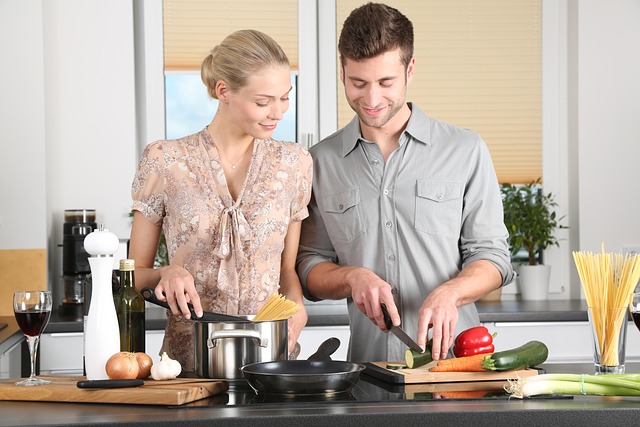
Cutting Precision
Understanding Cutting Precision
In a world where everything seems to be getting faster, sharper, and more efficient, cutting precision has emerged as the unsung hero of the industrial landscape. Think about it: whether you're crafting a delicate piece of art or fabricating components for a rocket ship (no pressure), the precision of your cuts can make or break the entire project. So, let’s dive into the nitty-gritty of cutting precision and why it matters more than ever.
What is Cutting Precision?
Cutting precision refers to the accuracy and quality of cuts made in various materials, be it metals, plastics, or even the occasional piece of glass (if you’re feeling brave). It’s not just about making a cut; it’s about making a cut that is exactly where you want it, with minimal waste and maximum efficiency. The goal? To achieve the perfect balance between quality and cost-effectiveness.
Why Precision Matters
Imagine you’re building a piece of furniture, and you accidentally cut a board too short. What do you do? You either start over or attempt some creative woodworking magic that usually ends in disaster. Precision cutting helps avoid those cringe-worthy moments. Here are a few reasons why it’s crucial:
- Quality Control: High precision means fewer defects and a superior finish. Nobody wants to buy a table that wobbles like a three-legged dog.
- Cost Efficiency: Accurate cuts minimize waste, which means you save money. And let’s face it: who doesn’t love saving a few bucks?
- Versatile Applications: From aerospace to architecture, precision cutting is vital across various industries. If it can be cut, it can be done precisely.
- Innovation: With advancements in cutting technology, the possibilities are endless. You can cut complex shapes and designs that were once thought impossible.
How is Precision Achieved?
Now that we know why cutting precision is important, let’s talk about how it’s achieved. Enter the world of waterjet cutting. This technology uses high-pressure water mixed with abrasives to slice through materials with astonishing accuracy. It’s like having a ninja with a water gun—silent but deadly.
Waterjet cutting can handle a variety of materials, including metals, plastics, stone, and even ceramics. It’s particularly useful because it doesn’t heat the material, which means there’s no risk of warping or altering the properties of what you’re cutting. Talk about a win-win!
The Future of Cutting Precision
Looking ahead, the future of cutting precision is bright. With the rise of automated cutting systems and AI technology, we’re on the brink of a cutting revolution. Imagine a world where you can design a component on your computer, send it to a machine, and watch as it gets cut to perfection while you sip your coffee. Sounds dreamy, right? ☕
In conclusion, cutting precision is more than just a technical term; it’s a vital aspect of modern manufacturing and craftsmanship. Whether you’re a DIY enthusiast or a business owner, understanding the importance of precision can elevate your projects to new heights. So next time you pick up a saw or a waterjet cutter, remember: measure twice, cut once—and maybe throw in a little bit of ninja magic.
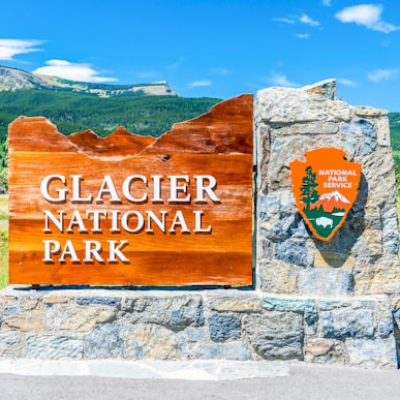